Get Reactive
Glass is made from sand, limestone and sodium carbonate. To get stained (colored) glass, other minerals are added.
Because these minerals are in the glass, they can react with one another when they come in contact. Some products have been developed for just that purpose. Oceanside has frit and glass called Red Reactive transparent and Red Reactive opal. It will react with any glass that has copper in it. It will give a deep reddish color where the reactive frit and copper-bearing glass intersect.

Oceanside Compatible Red Reactive Opal Coarse Frit 96 COE (stainedglassexpress.com)
Oceanside Compatible Red Reactive Opal Frit Fine 96 COE (stainedglassexpress.com)
Oceanside Compatible Red Reactive Opal Frit Medium 96 COE (stainedglassexpress.com)
Oceanside Compatible Red Reactive Opal Powder Frit 96 COE (stainedglassexpress.com)
Oceanside Compatible Red Reactive Transparent Frit Coarse 96 COE (stainedglassexpress.com)
Oceanside Compatible Red Reactive Transparent Frit Fine 96 COE (stainedglassexpress.com)
Oceanside Compatible Red Reactive Transparent Frit Medium 96 COE (stainedglassexpress.com)
Oceanside Compatible Red Reactive Transparent Frit Powder 96 COE (stainedglassexpress.com)
Oceanside Red Reactive Opal Stringer 96 COE (stainedglassexpress.com)
Oceanside Red Reactive Transparent Noodles 96 COE (stainedglassexpress.com)
Oceanside Red Reactive Transparent Stringer 96 COE (stainedglassexpress.com)
Sulfur-bearing products will also react with copper bearing products. The link below will bring you to Oceanside’s Reactive charts.
Reactive Guide – Oceanside Art Glass (oceansidecompatible.com)
Vanilla Cream is a high sulfur content glass that is also reactive, it even changes from within. After full fusing the inside of the glass stays its pre-fused off-white color while the outside brightens to a vivid warm white.
Oceanside Vanilla Cream Opal Glass (stainedglassexpress.com)
Bullseye also has reactive products.

Bullseye Reactive Cloud Opal Frit- Medium 90 COE (stainedglassexpress.com)
Bullseye Reactive Cloud Opal Frit- Powder 90 COE (stainedglassexpress.com)
This is a link to the Reactive Potential of Bullseye Glass. It is truly amazing and very fun to play with these combinations.
Reactive Glass Chart.pdf (amazonaws.com)
Glass Pigments
Compounds | Colors |
iron oxides | greens, browns |
manganese oxides | deep amber, amethyst, decolorizer |
cobalt oxide | deep blue |
gold chloride | ruby red |
selenium compounds | reds |
carbon oxides | amber/brown |
a mix of manganese, cobalt, iron | black |
antimony oxides | white |
uranium oxides | yellow-green (glows!) |
sulfur compounds | amber/brown |
copper compounds | light blue, red |
tin compounds | white |
lead with antimony | yellow |
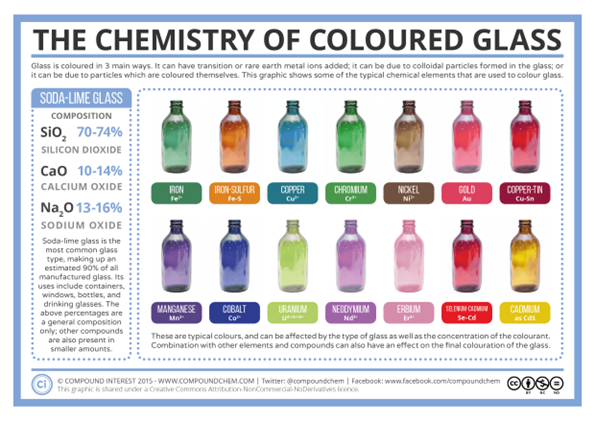






